Never Stop Building: Hardware Prototyping
Turn an idea into reality. With a broad spectrum of manufacturing and engineering skills, Never Stop Building is able to be a single source for product concepts and hardware prototypes. Validate your concept through rapid iteration, a craftsman’s attention to detail, and unyielding passion to create.
Electronics Prototyping
Integrate and test circuit components for IOT, Arduino, Raspberry Pi and more. Develop charging circuitry, power conditioning, cellular and WIFI connectivity.
Electrical Systems Design
Design and prototype wiring harnesses. Source fabrication. Design and fabricate custom enclosures for industrial automation, heavy equipment and control applications.
Power Systems Fabrication
Specify, design and build off grid solar and power redundancy systems. Source components and create robust systems for harsh environments.
Expert Class CAD Modeling
15+ years experience with Autodesk Inventor Parametric CAD suite. Translate sketches to full 3D models with production drawings. Model pipe and wiring systems.
PCB Design and Fabrication
Create electronics schematics, place components and route traces. Prototype and test boards. Source fully assembled PCB with components.
Engineering for Fabrication
Design parts per client specifications. Solve design problems to achieve customer goals. Create shop drawings and source fabrication. 3D Print prototypes for rapid iteration and feedback.
Process
In order to realize the client’s goal, a variety of technical components will need to be selected, integrated, and tested. Additionally, often control software must be developed to breath life into the creation. Though nearly all goals are technically feasible, the risks inherent to the project will always boil down to the uncertainty in component and development costs, and the time required to build the prototype.
To mitigate these risks, we suggest an iterative approach that will endeavor to quickly produce “something that works”, and continuously improve the device. Constant feedback on each iteration will ensure the project stays on track.
1. Discovery Phase
Gather requirements, conduct research, develop execution plan and project scope. Estimate total project budget.
2. Prototype Phase
Execute on prototype development, creating design collateral and working prototype for customer validation.
3. Pre-Production Phase
Develop improved prototypes and documents to move to production run. Interface with vendors and third parties.
Case Study: RFID Personnel Tracking
Our client came to us with this picture and an idea. Could we use RFID tags and long range antennas to track the comings and goings of personnel on large scale construction projects? Non-intrusive monitoring would mean reduced push-back to implementation and provide data that project owners would use to determine if the building was on schedule.
Our approach took us from quickly integrating off-the-shelf hardware to a fully custom unit along with web based management software. Please see the slide show below for details on the project.
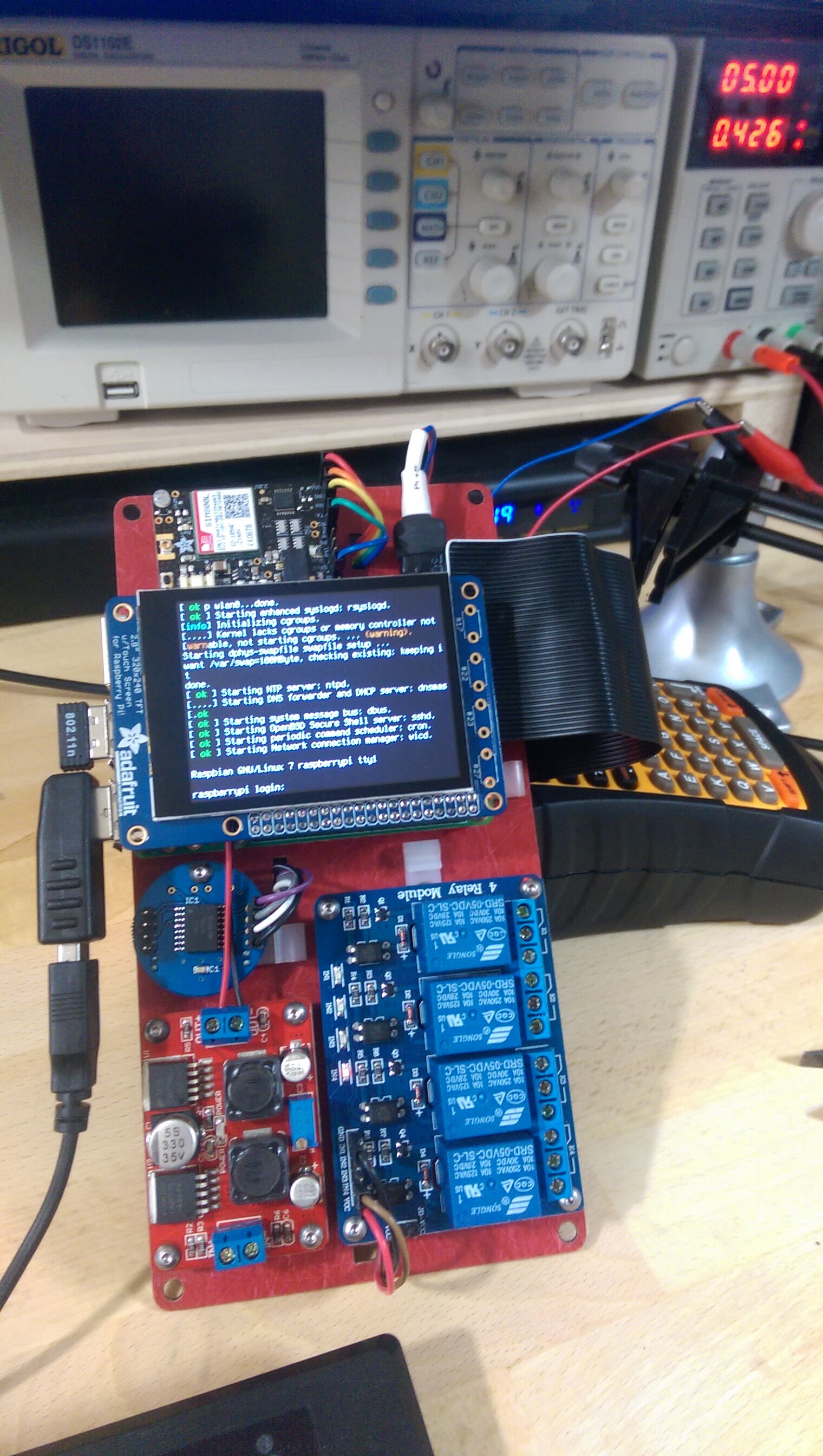

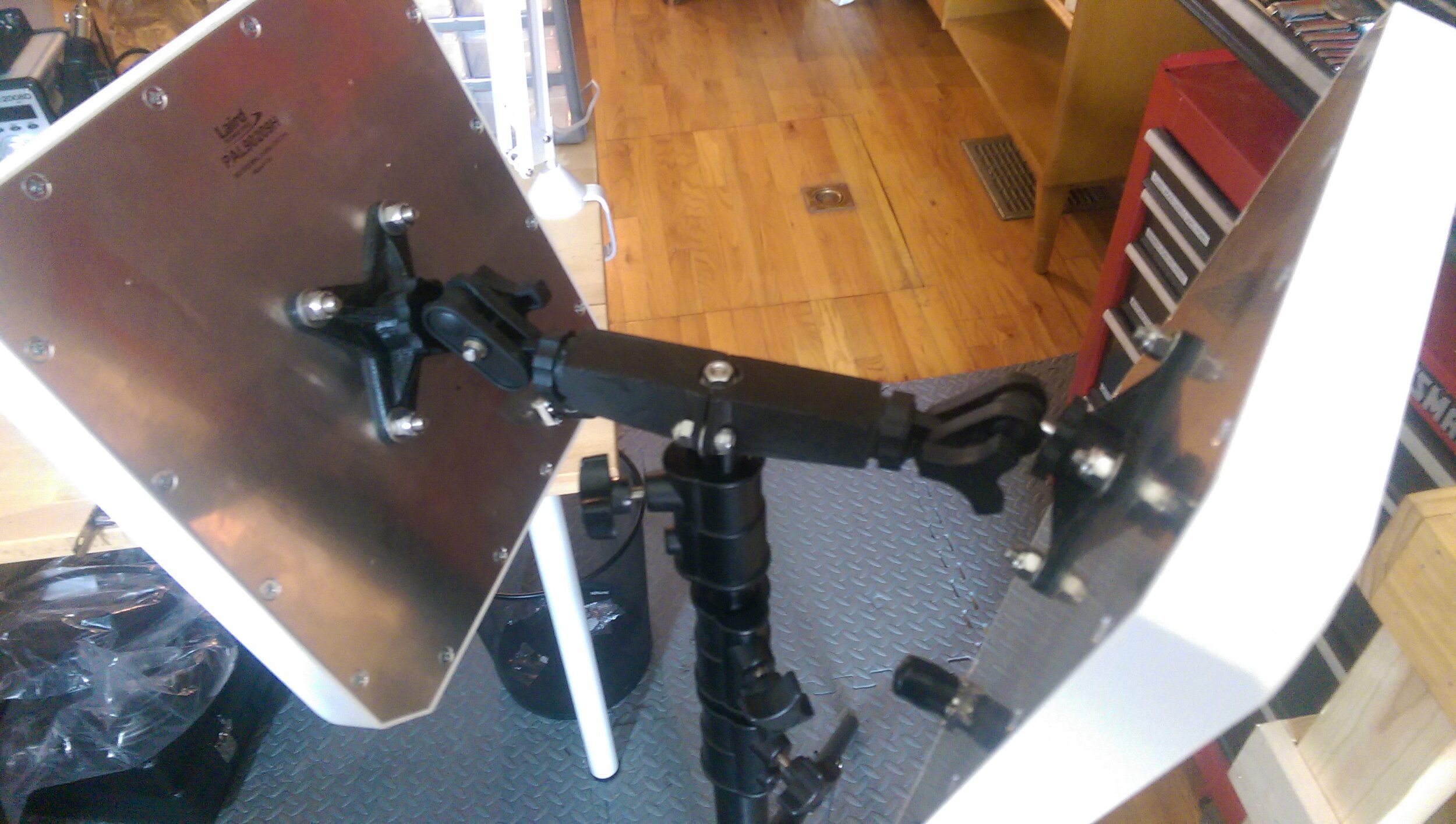
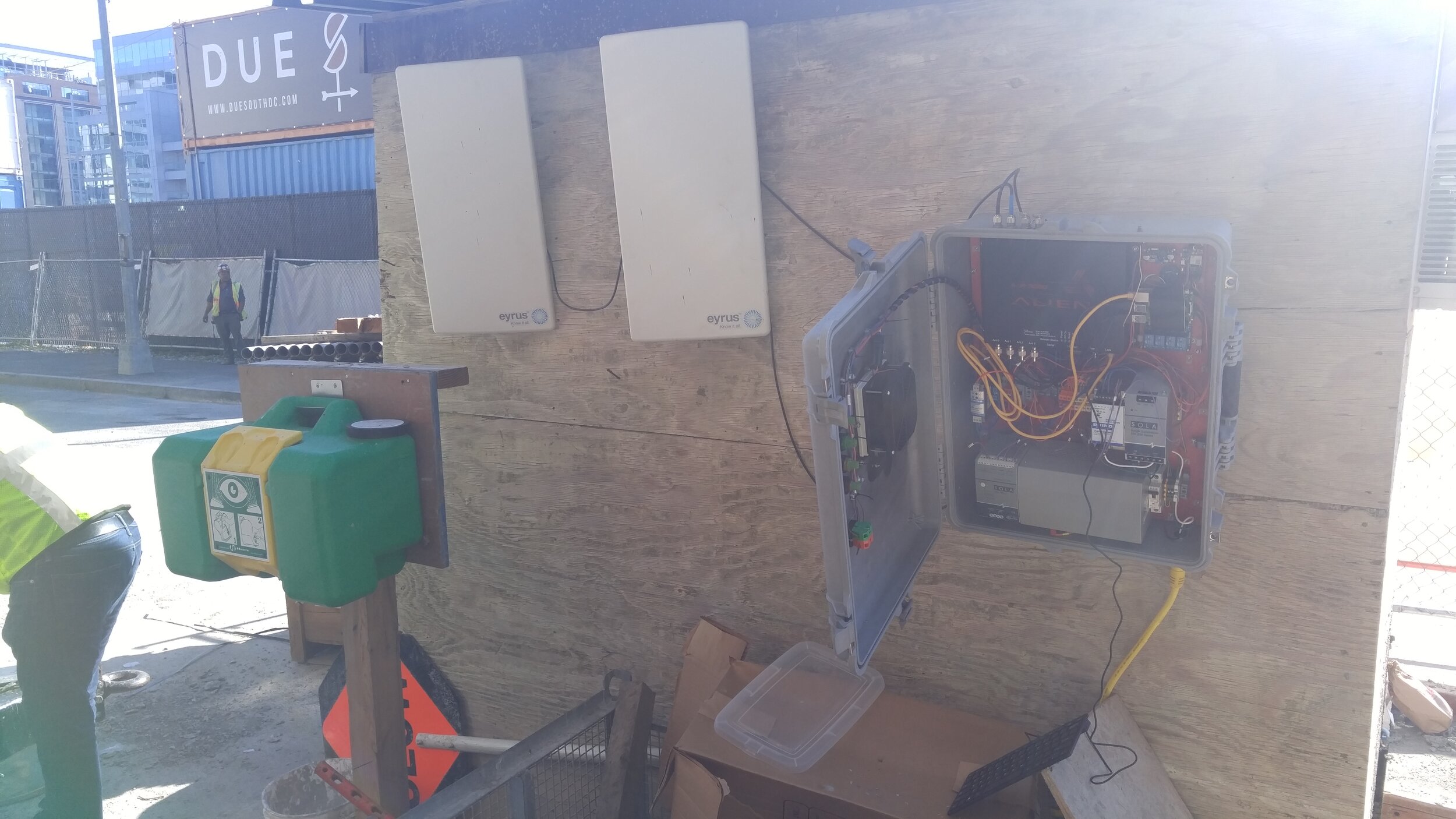
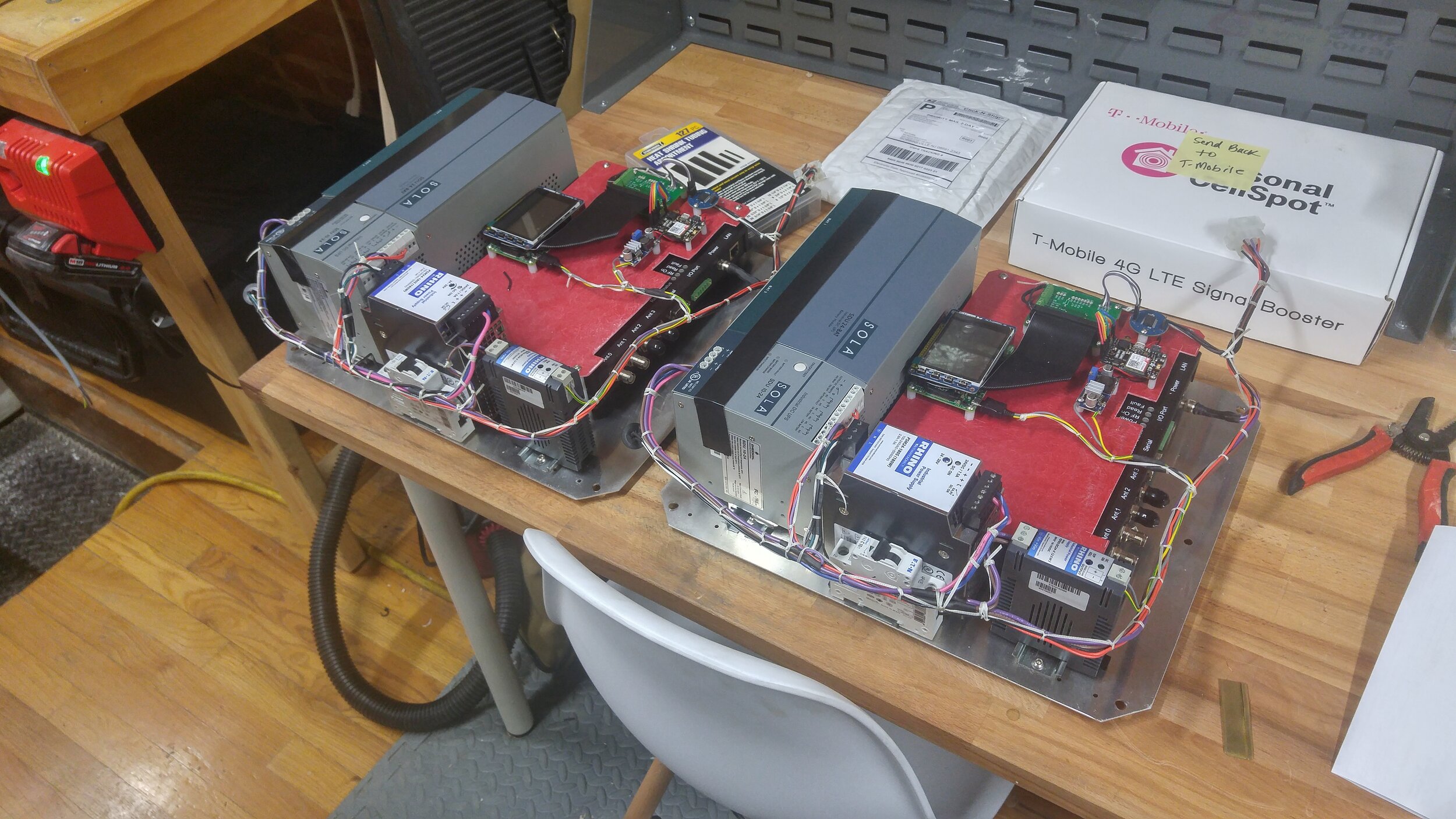
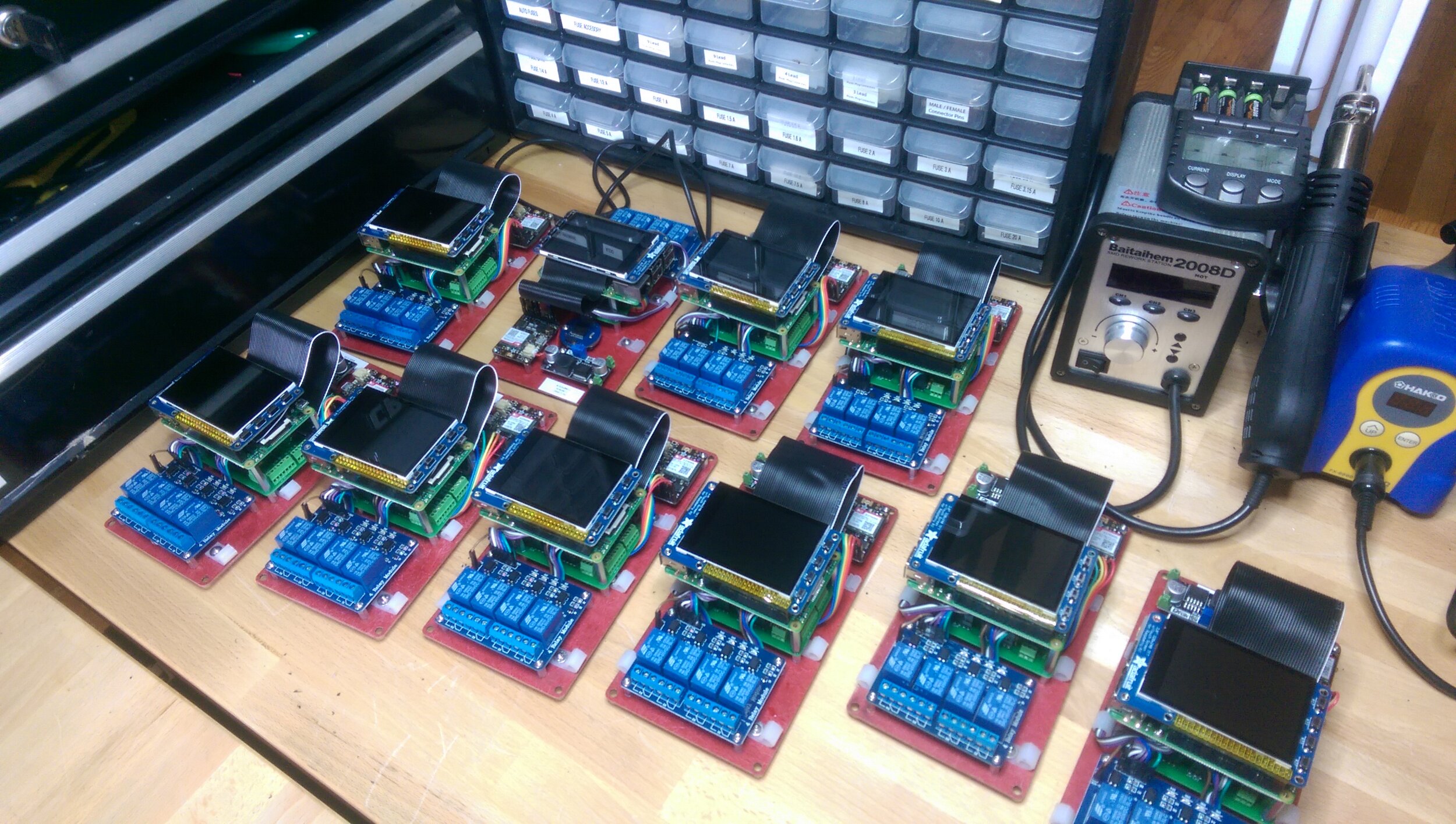
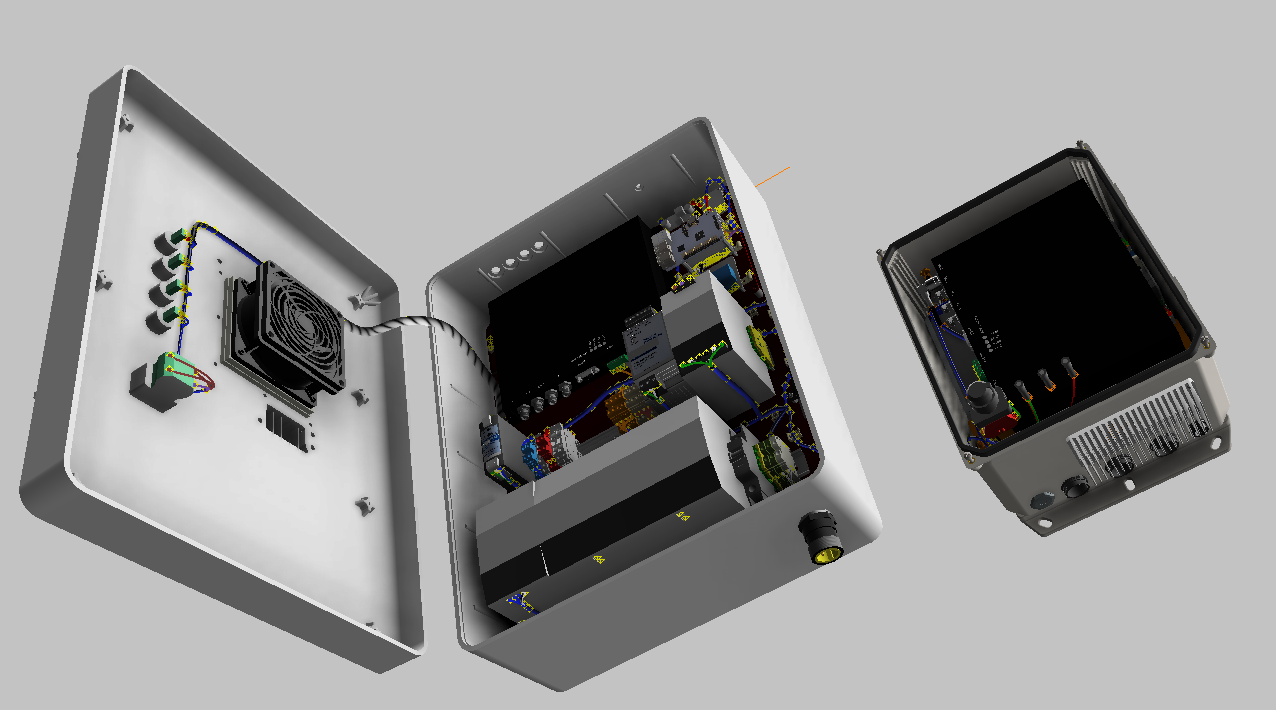
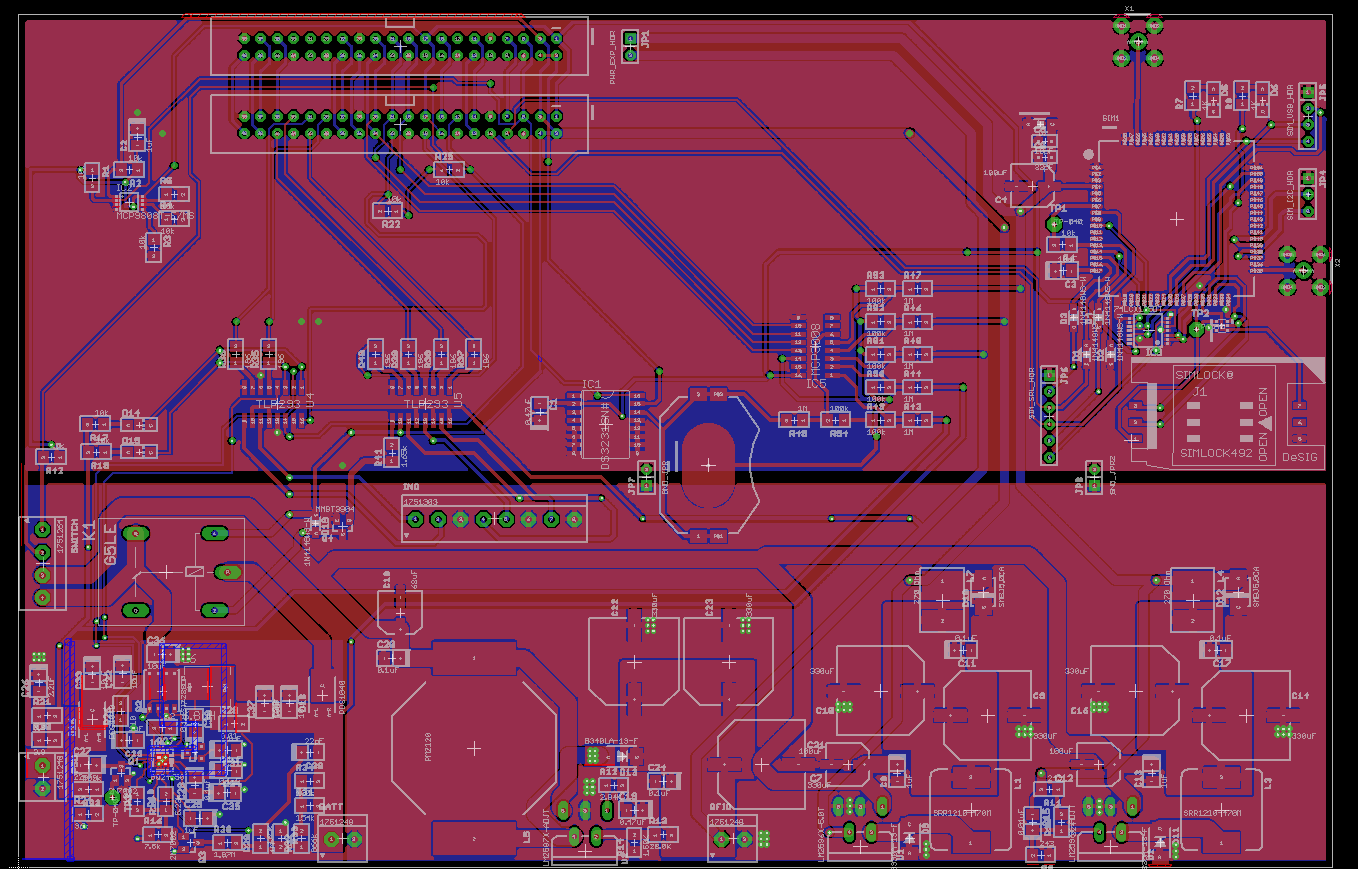
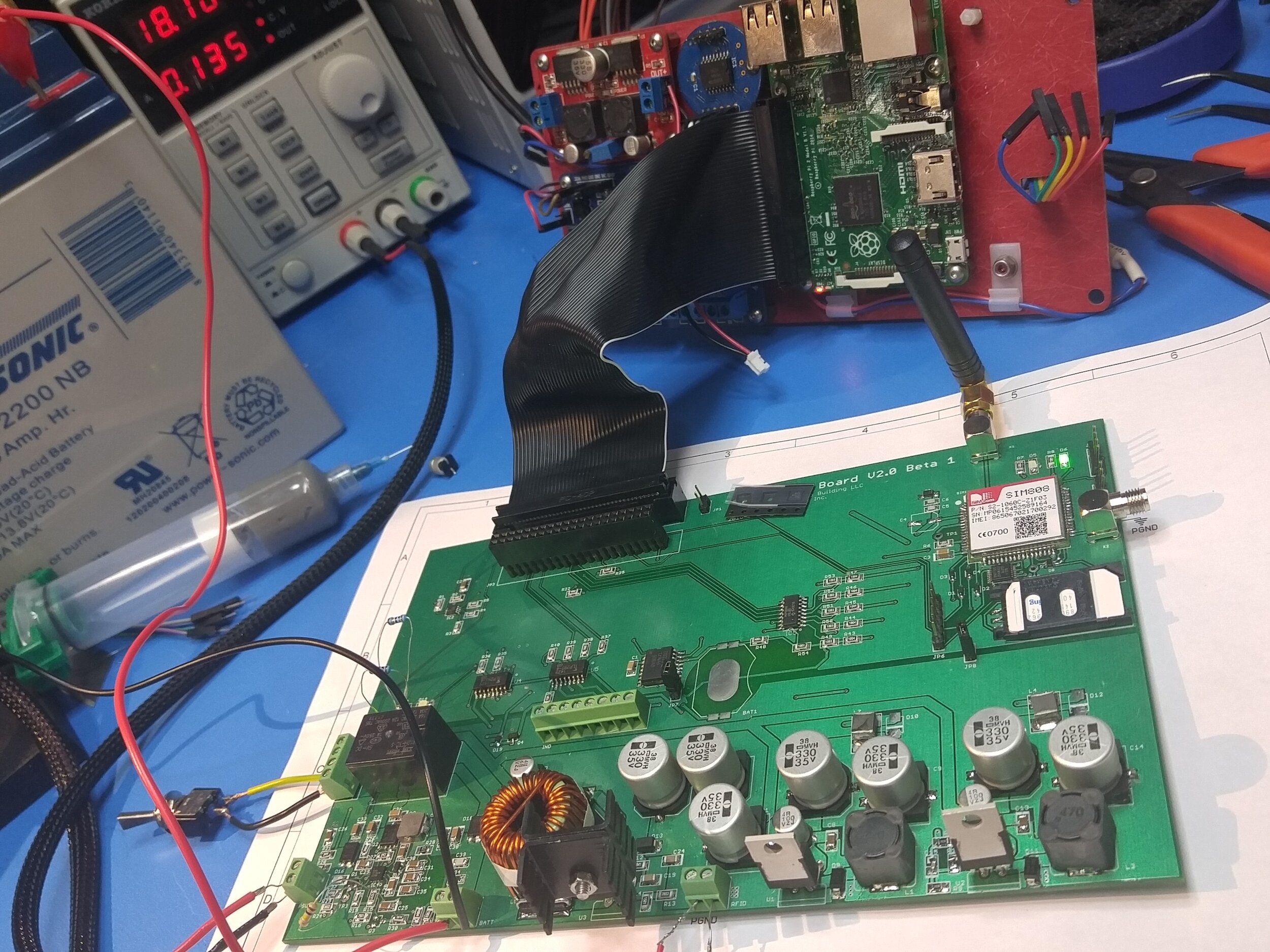
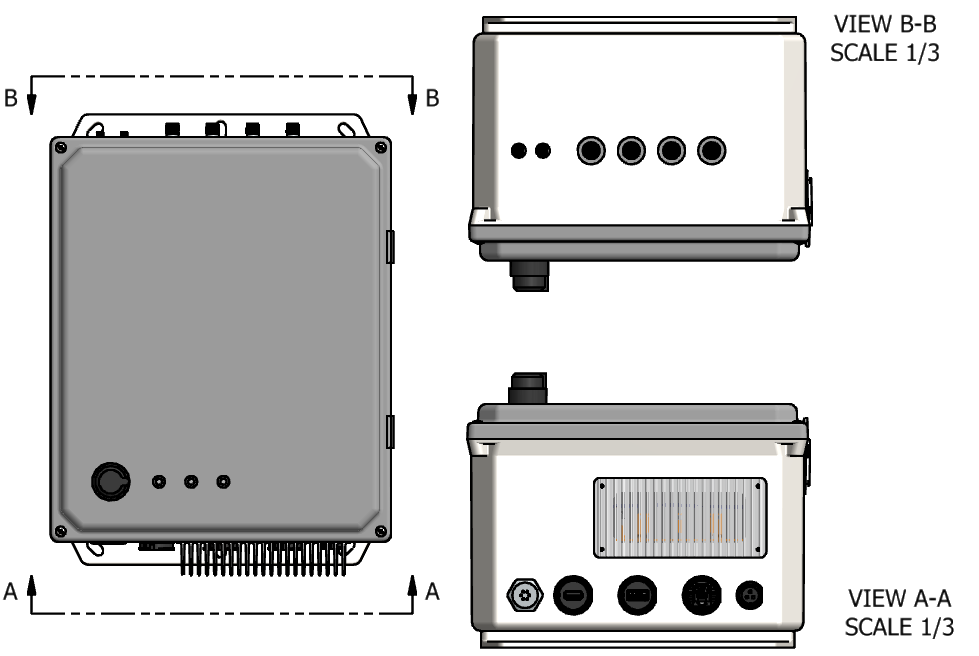
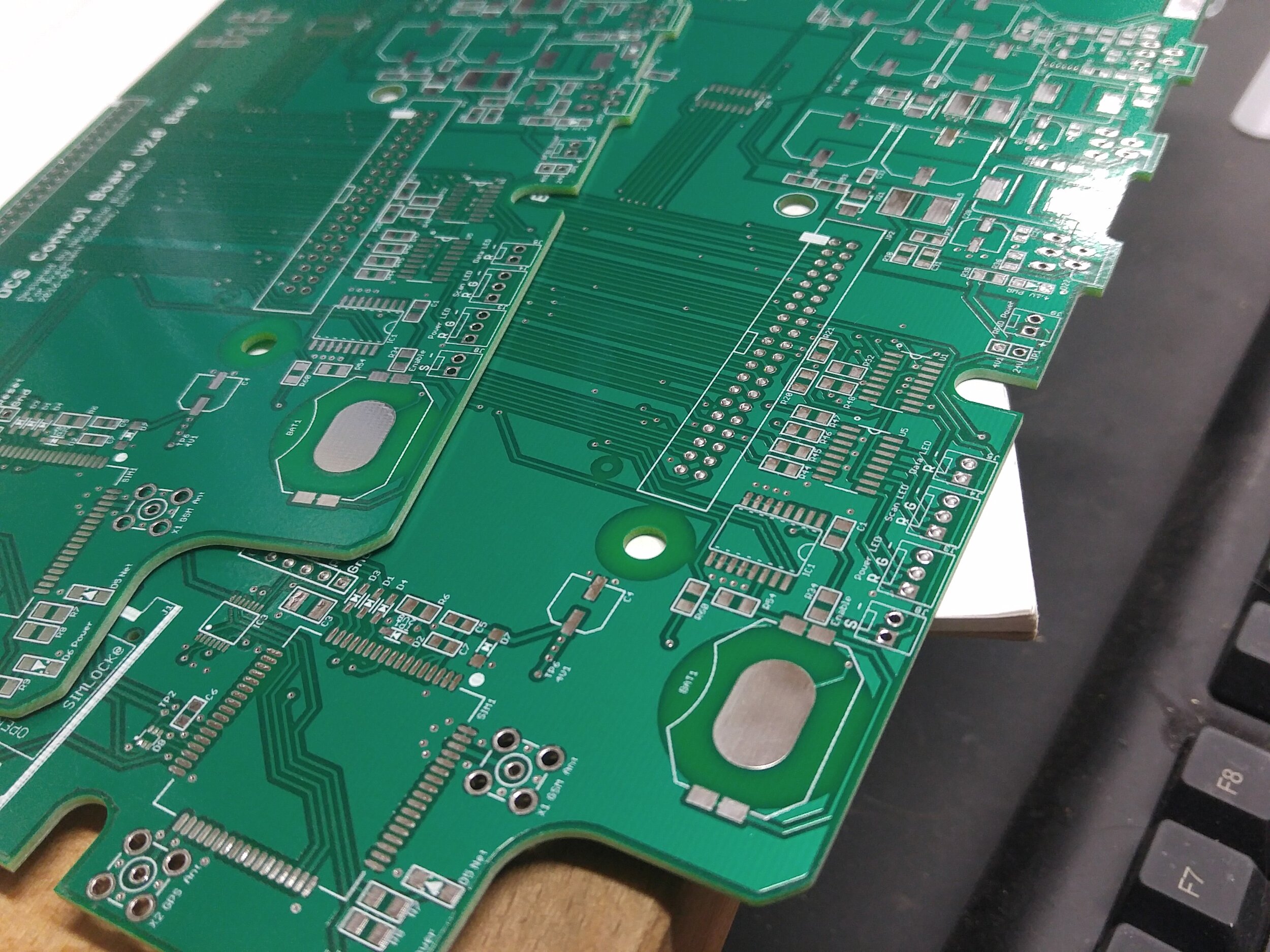
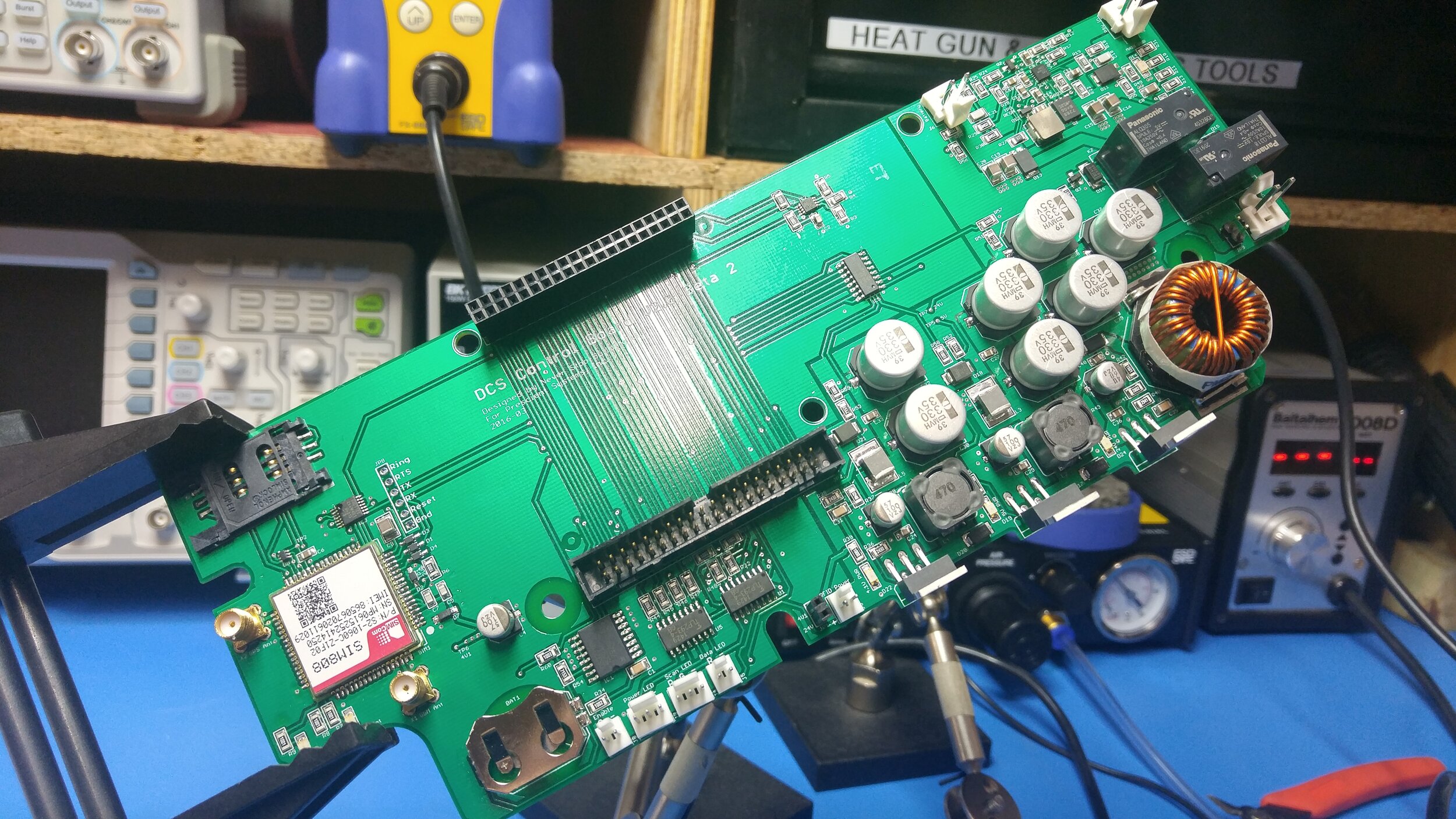
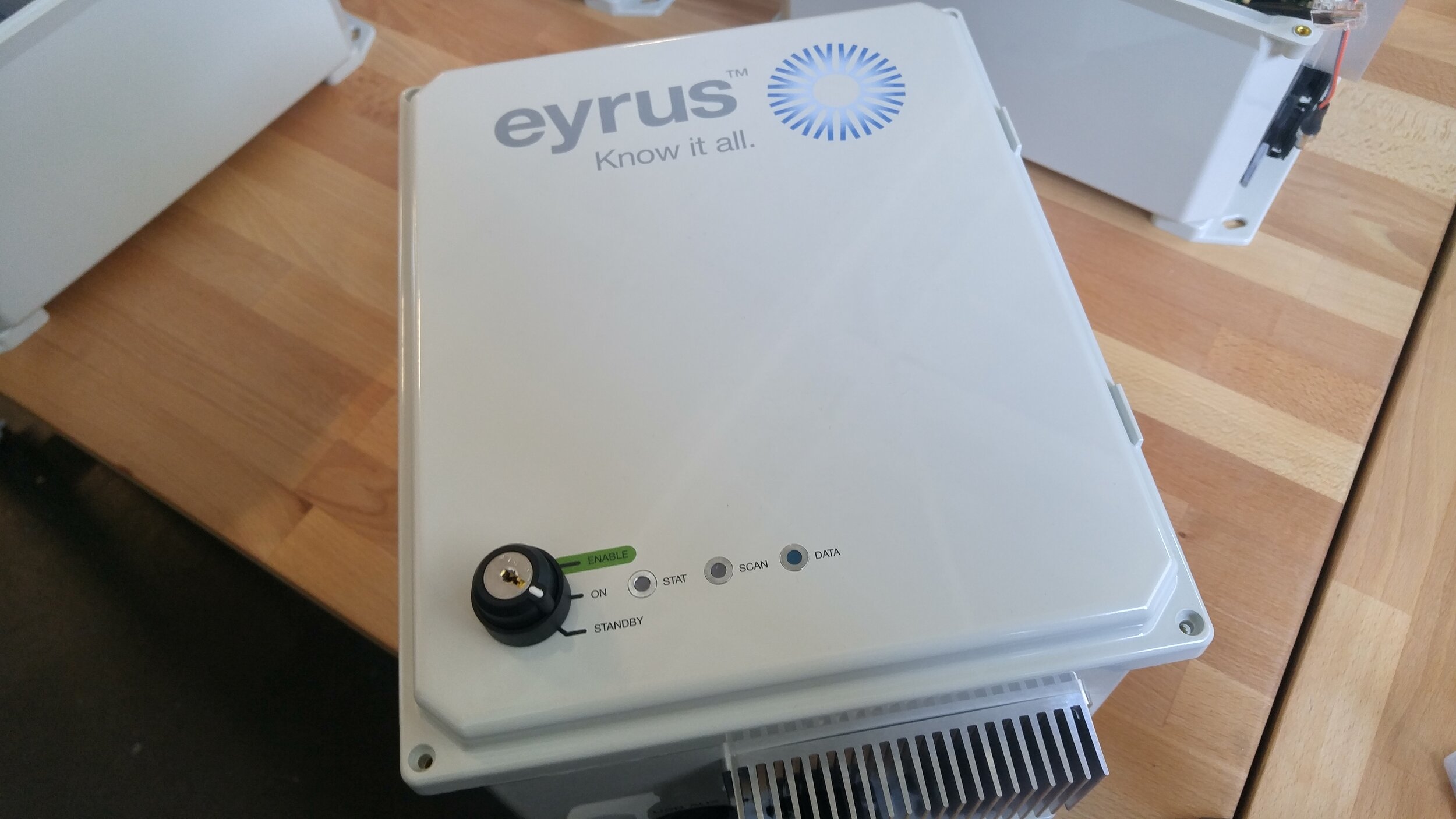
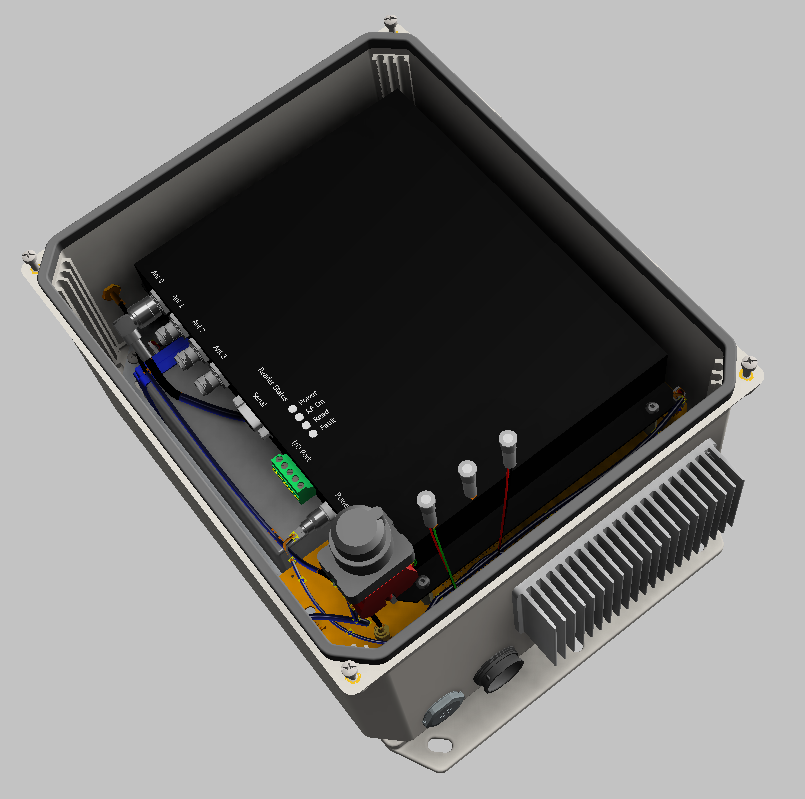
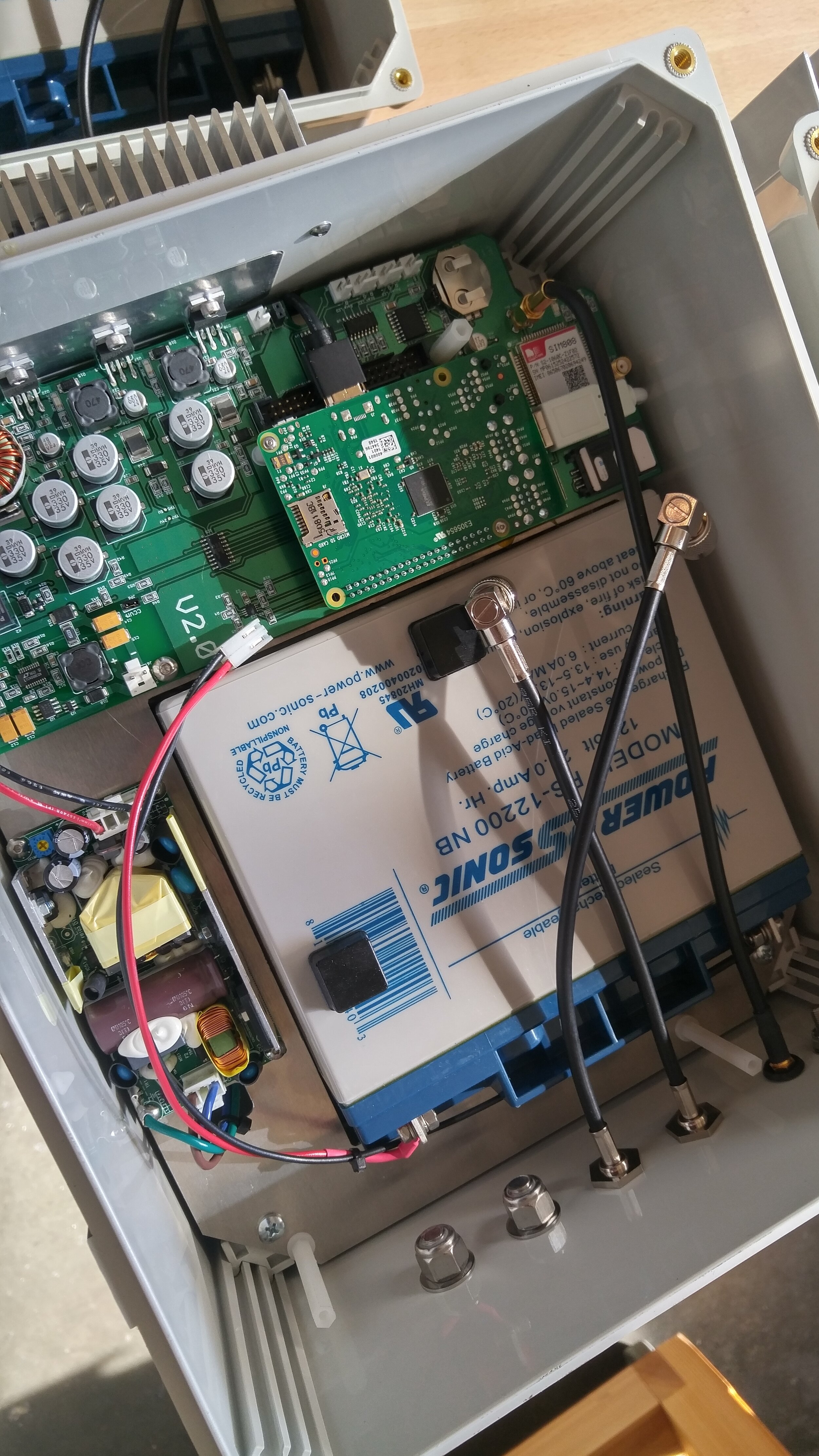
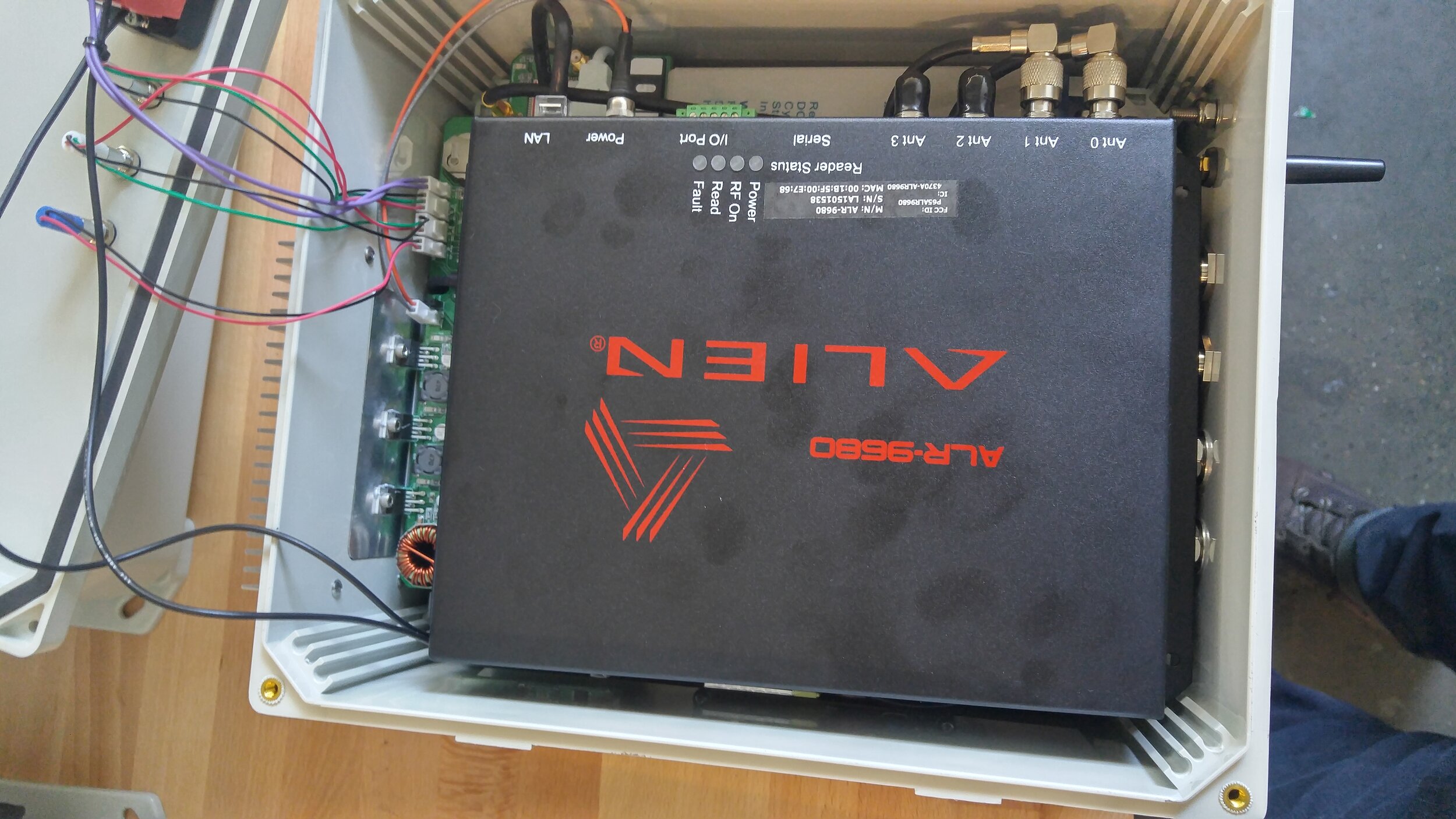